Established in 1977 and employing over 300 people, Hydram Engineering is one of the largest sheet metal fabrication companies in Europe. It offers the full range of engineering services including laser cutting, CNC punching, panel bending and folding, tube laser cutting and tube bending, fabrication, powder coating, wet painting and assembly from its 130,000 square foot facility in Chilton, County Durham, UK. Hydram Engineering supplies metal enclosures, components and precision sheet metal fabrications to market-leading companies in industries such as railway, public transport, off-highway vehicles, defence, renewable technologies and furniture.
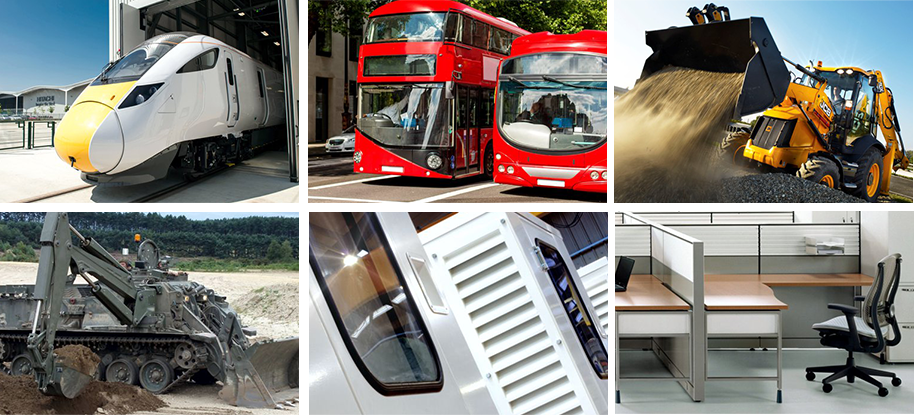
As one of the UK's largest sheet metal companies, Hydram operates three Bystronic laser cutting machines and two Trumpf punching machines, all of them complete with tower storage and full automation. The manufacturing plant also includes a total of fourteen multi-axis pressbrakes, three robotic welding cells, two tube-cutting lasers, and three powder coating lines. The machinery runs five days a week on a 24-hour basis, with additional partial weekend operation too, so there are significant challenges in not only maintaining production on tight deadlines, but also ensuring optimal operation of each element of the factory to maximise resources, schedules and staff. With this in mind Hydram Engineering have employed IT infrastructure in various forms to deliver efficiencies and help innovate for the future.
Digital Transformation within Hydram Engineering
The company has embraced and deployed a number of solutions that have offered enhancements to how its facilities run, improving how performance and target metrics are viewed and how information is shared within the organisation.
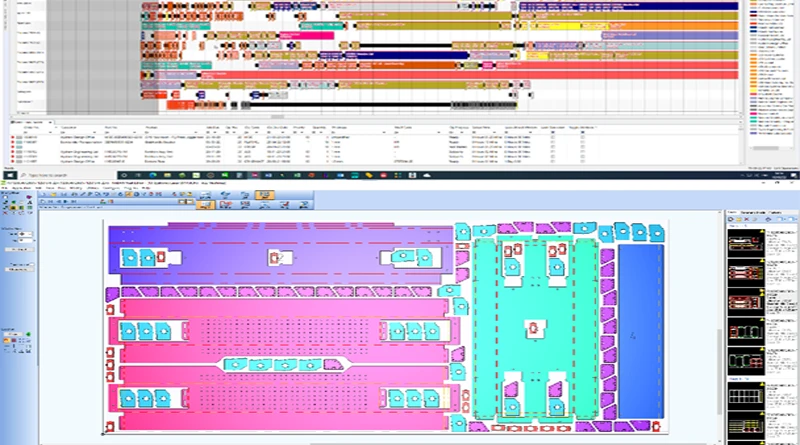
Advanced Scheduling
Cutting sheet can be wasteful of time and resource if constantly swapping materials, so advanced nesting and scheduling software applications are used to look ahead in the production schedule in real time and allocate jobs together that ensure maximum utilisation of a single sheet of metal with minimal wastage. These applications run on high performance workstations, server and storage hardware in order to deliver the scheduling data in the most timely manner as cutting operations take place.
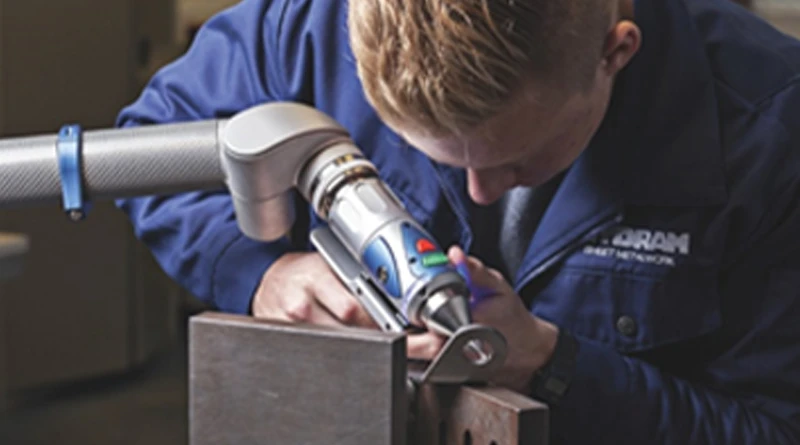
Inspection
During production, quality control is key to saving time and costs and technology is employed in different ways. Hydram uses 3D measurement contact arms which can compare actual measurements from finished components with CAD 3D models embedded with geometric dimensioning and tolerancing information up to an accuracy of 10 microns. Vision inspection systems are also deployed to look for facets of any given component to ensure it is correctly manufactured and without fault. Controlled by a GPU-accelerated workstation, a matrix of seven cameras captures every angle to allow comparison with feature libraries of good components. This process relies on high performance servers and storage to access the correct component data in real time.
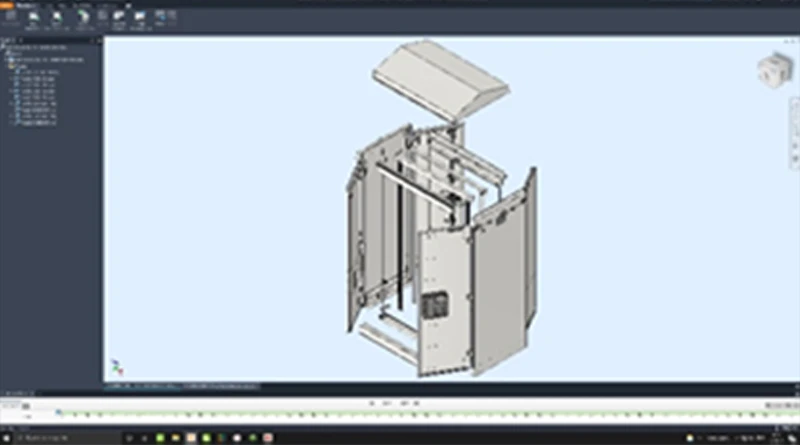
Design
As part of the manufacturing process for market-leading clients, it is often vital to understand how an existing component is designed and crafted, so it can be replicated with maximum speed and efficiency. 3D modelling software running on high-performance workstations allows engineers to create digital reproductions of large assemblies right down to the last nut and bolt. A single product can have several hundred subcomponents and to maximise their productivity the engineers benefit from high performance servers and storage.
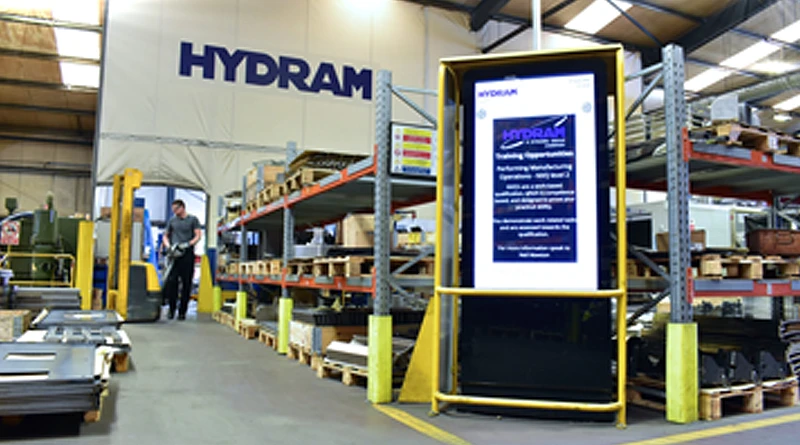
Monitoring
In order to more clearly show production targets, schedules and job resources, digital signage has been employed on the shop floor in the form of free-standing totems and wall mounted screens. These can be centrally controlled to show a variety of analytics, key performance indicators and even information such as who are the first-aiders on duty. Their multi-functionality is also extended to a marketing capacity when visitors are being shown around the manufacturing facilities.
Potential Future Innovation
Hydram Engineering is always looking for new and innovative ways to enhance productivity, and efficiency. One possible future development being considered is the introduction of AI technology into their production line inspection capabilities, thus removing the need to create the faceted model for the system to base its assessment on. Instead an AI algorithm could be trained to learn what faults may occur as well as potentially being used in a predictive maintenance capacity on the production line itself.
The Scan Partnership
Scan has been a trusted advisor to Hydram Engineering since 2015, providing workstation, server, infrastructure and digital signage solutions. The latest systems installed in 2022 include custom designed servers based on 3rd gen AMD EPYC CPUs.
Project Wins
Reduction in production costs due to improved resource utilisation
Reduction in downtime due to predictive maintenance sensors on production lines
Improved communication of schedules and deadlines across the shop floor
Featuring comprehensive warranties and being competitively priced also helped as due to the scope of the project, additional quotes were required for comparison - however Scan was still the partner of choice.
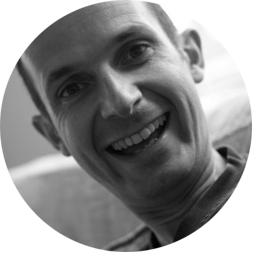
Andrew Jordan
Systems and Technical Manager, Hydram Engineering
"We rely on Scan for their attention to detail, flexibility and ability to supply the latest technologies at competitive prices. Our new server purchases have the latest Gen4 NVMe storage systems which have eliminated transaction bottlenecks and will allow our databases and network to continue grow with the business in future with zero impact on performance."
Speak to an expert
You’ve seen how Scan has helped Hydram Engineering take advantage of digital transformation technologies in their business. Contact our expert teams to discuss any requirements or discuss any projects you have.
phone_iphone Phone: 01204 474747
mail Email: [email protected]